
The key piece of manufacturing DX completion
With data management support that automatically collects and analyzes core operational data, we save 275 trillion ₩ in wasted costs each year.
Reduce data input resources & resolve human errors
By automatically entering data, we reduce resources previously consumed by manual and hand inputs and minimize human errors.
Fast and easy data extraction with 1Day data collection infrastructure setup
Once the sensor is installed, data collection begins immediately, allowing for quick data verification and innovatively shortening the augmentation operation period.
High-density data real-time collection
Through high-density data collection with a data transfer cycle of 2 seconds, it is possible to know the factory status more accurately and in more detail compared to the existing collection method.
Centralization of equipment data without being bound by manufacturers
Data centralization without affecting equipment warranties, through data collection via sensors with non-invasive installation methods, regardless of the manufacturer.
Why do we need a factoroid in MES?
Project duration
3 mos. shortened
9 mos.
6 mos.
Facility interface cost
Save 100 mn ₩
400 mn ₩
300 mn ₩
Real-time streaming of factory conditions through AI algorithms
AI voucher official certification algorithm
Streaming data
Configuration
Self-powered wireless sensor
Uninterrupted facility easy installation
|
Facility non-intrusion
|
Real-time
FACTORIOD has realized wireless sensorization through energy harvesting technology using various power sources (current, magnetic field, light, vibration, etc.) and wireless communication technology. Through these sensors, it collects various data from the production site in real time, such as equipment operation information and power usage.
Smart DB
General AI
|
Cloud
Continuously learning AI-powered smart DBs collect raw data through sensors and transform it into the necessary data for factory management, storing it. Currently, Gentle Energy operates various customer manufacturing data through this smart DB totaling 2TB.
Dashboard UI
Real-time streaming
|
web dashboard
We provide a dashboard that allows you to easily check the operating information, power usage, and production information of essential equipment in the production site. You can also check the current operating status of the factory through real-time factory streaming function, and the streaming data is stored in the database for statistical confirmation for the desired period and organizational unit. This dashboard is provided in web format and can be accessed from any internet-based device, including smartphones.
AI consultant
(Coming Soon)
Automatic Report
|
Insight extraction
Consultant who creates automated daily/weekly/monthly reports and provides data-driven answers to users' questions through Chat GPT-based generative AI.
Applied effect
MES / ERP supplier
End user (Factory)

PoV service
Are you hesitating to introduce the service?
We provide PoV (Proof of Value) services at minimal cost so that you can experience the benefits of the service.
Apply
Use case
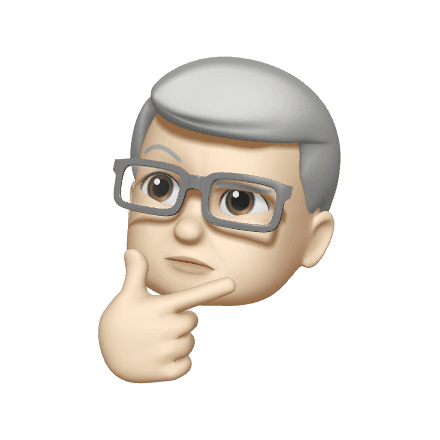
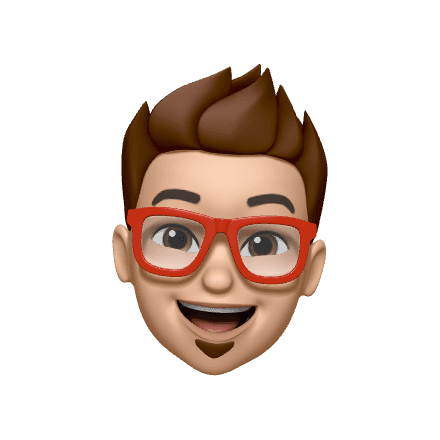
